Introduction - The Importance of Process and Data Orchestration
Manufacturing in the Pharmaceutical, Food, Fast Moving Consumer Goods (FMCG) and Chemical industries is undergoing a radical transformation, driven largely by the accelerated adoption of digital technologies. Amongst these changes, electronic batch release (EBR) and process & data orchestration have emerged as indispensable approaches, improving efficiency, compliance, and traceability.
Electronic Batch Release: A Paradigm Shift
Batch release, a vital step in manufacturing, is traditionally conducted manually, often leading to inefficiencies (slow down of the process), errors (missing data/wrong data), and regulatory complications (process gaps/data integrity). It may shock people, but many organisations still use paper or spreadsheets to manage their batch release processes and tracking. The introduction of electronic batch release has marked a significant shift in this landscape. EBR solutions facilitate a more streamlined, automated, data-driven process, eliminating manual errors and enhancing process efficiency.
Furthermore, EBR improves data integrity, a crucial factor in maintaining compliance with regulatory authorities like the U.S. Food and Drug Administration (FDA) and the European Medicines Agency (EMA). By digitising batch records, the EBR process can become digitalised, ensuring complete transparency and traceability in the batch release process, simplifying audit procedures and ensuring regulatory compliance.
The Role of Process and Data Orchestration
One significant contributor to the growing effectiveness of EBR systems is the integration of process and data orchestration capabilities. Process orchestration acts as a conductor, synchronising various tasks, streamlining workflow steps, and managing exceptions, thus promoting efficient and seamless operations.
Process orchestration in EBR provides a comprehensive, real-time view of batch release processes, enabling companies to control and optimise their operations better. It ensures that the right task is assigned to the right person at the right time, thereby minimising errors, reducing cycle time, and increasing productivity. Data orchestration ensures the right data is moved from one operational system to another in sequence according to the release process, ensuring chain of custody and data integrity.
Moving data through the process from the initial “batch release request” in ERP (Enterprise Resource Planning) to LES (Laboratory Execution System) to LIMS (Laboratory Information Management System) to a given INSTRUMENT then INSTRUMENT back to LIMS back to ERP for checking that the data/results meet the product specification and business rules is an area where process and data orchestration tools like BPO (Business Process Orchestration) and the associated BPMN (Business Process Model Notation) approaches can dramatically impact operational efficiency, insight and integrity.
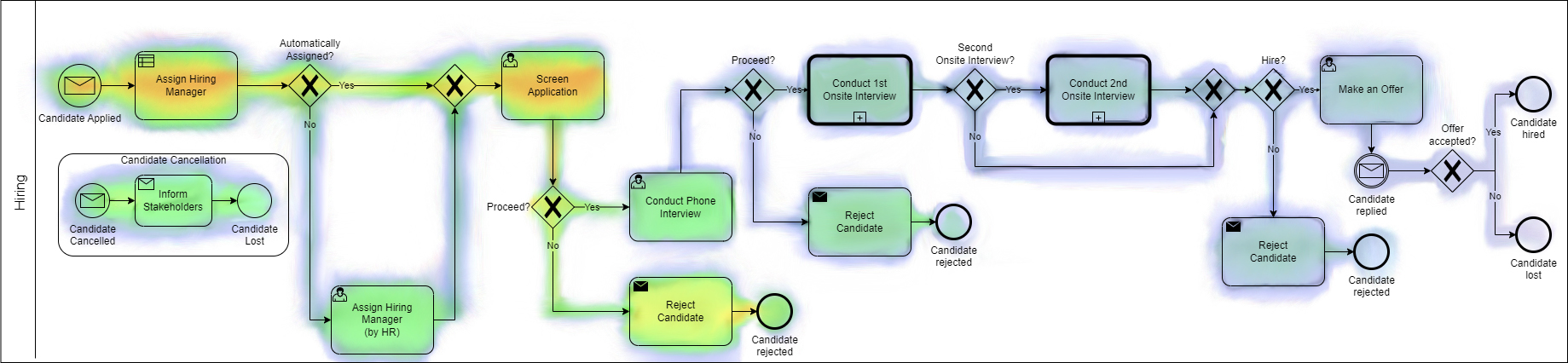
Figure 1. Example of a Camunda (BPMN and BPO platform) process heat map view showing areas of focus.
BPMN tools allow organisations to keep their current infrastructure and systems, which are validated and integral to their process, and leverage them more effectively: removing manual / semi-manual movement of data through the process and gaining valuable insight into where every function, lab test, and result is in real-time. This means manufacturer plants can see where a batch is at any time – allowing them to plan and predict more effectively.
Moreover, process orchestration tooling allows for a high level of flexibility. It provides a framework that can easily adapt to regulatory requirements, changes in product specifications, manufacturing processes and company policy changes, supporting continuous improvement and scalability whilst maintaining compliance and integrity.
The Impact of EBR and Process Orchestration on Quality Control
In the pharmaceutical industry, quality control is paramount. By leveraging EBR and process orchestration, manufacturers can enhance their quality control measures. With real-time visibility into operations and automated workflows, companies can quickly detect and resolve quality issues, reducing the risk of non-compliance and dreaded product recalls.
Additionally, these technologies offer robust analytical capabilities. Manufacturers can identify trends, predict potential problems, and make data-driven decisions to improve product quality and efficiency by aggregating and analysing data from various stages of the batch release process.
One area these technologies are super critical is in the Cell and Gene Therapy space. Here, the process of manufacture is:
- Super time critical – the regulated production process is required to be executed and completed in days and weeks, rather than months or years
- Very complex – as the manufacturing process typically leverages biological systems adapted based on the specific type of therapy for a particular patient
- Dependent on process precision and accuracy – any “gaps” in product quality or precision can result in catastrophic implications for the patient
- Potentially localised in hospitals – as the time taken to send biological samples to a “site” is not feasible
- Temperature dependent sample logistics – as some manufacturing has to be done elsewhere and biological samples must be temperature controlled at -80oC
With these requirements – the common paper and spreadsheet data tracking and manual process control are not appropriate or even tenable as the data and sample chain of custody requirements are too stringent.
The Road Ahead
As we navigate towards an increasingly digitised future, the role of technologies like EBR and process orchestration (BPMN) in manufacturing will continue to evolve. They will drive operational efficiency (batch throughput) and enable companies to maintain the highest safety and quality standards.
Artificial Intelligence (AI) and Machine Learning (ML) are expected to be increasingly prominent in this space. Leveraging AI and ML, future EBR systems could predict and prevent manufacturing errors, optimise batch release processes, and provide actionable insights for strategic decision-making.
Despite these promising developments, a successful digital transformation in manufacturing requires a thoughtful, holistic approach. It involves investing in advanced technologies and building a culture that embraces change, prioritises data literacy, and values continuous learning and improvement.
Conclusion
In conclusion, EBR and process orchestration are changing the face of manufacturing, offering a way to improve efficiency, compliance, and quality control. By adopting these technologies, companies can stay ahead of the curve, ensuring they are prepared to meet the demands of an ever-changing regulatory landscape and the ever-increasing expectations of humankind.
If you would like to know more about what Zifo is doing in this area please drop us an email at
info@zifornd.com.