Implementing LIMS in Manufacturing QC
A robust Laboratory Information Management System (LIMS) is crucial for streamlining manufacturing quality control (QC) processes and subsequent product batch release. A tailored LIMS enables efficient sample tracking, analytical testing, data organization, and reporting, ensuring process optimization, regulatory compliance and data integrity. Below is Zifo's step-by-step guide for successfully implementing a LIMS focusing on Manufacturing QC laboratories.
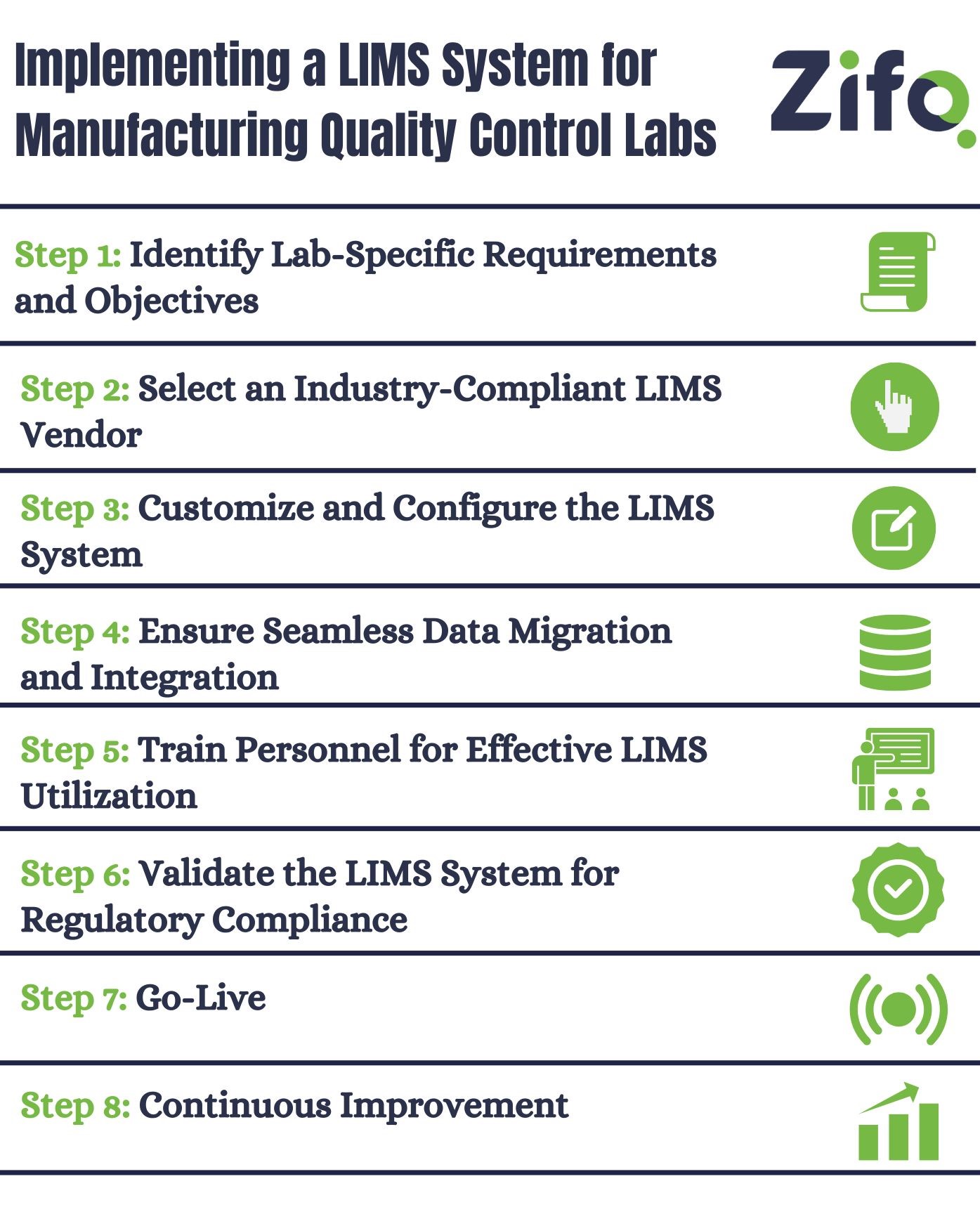
Step 1: Identify Lab-Specific Requirements, Workflows and Processes
Conduct a thorough assessment of your lab's unique requirements, processes, data orchestration workflows. Consider factors such as sample management, instrument integration, inventory management, regulatory compliance, and specific industry standards. Alongside the lab processes, consider how the system fits into the overall business process of product batch release. This evaluation will help you define the precise capabilities, processes and data orchestration workflow support needed to meet your lab's needs. It is also essential to consider the future and how things could be optimized further as you change to the new system.
Step 2: Select an Industry-Compliant LIMS Vendor
Research and choose a LIMS vendor with a proven track record of specializing in manufacturing QC. Look for vendors experienced in regulatory compliance, such as current Good Manufacturing Practices (cGMP) and 21 CFR Part 11. Evaluate their system's capabilities, scalability, support services, and user-friendly interfaces to find the best fit for your lab and ergonomics. The vendor must have a detailed roadmap and vision for their products. Ensure your vendor has a good strategy to deliver/integrate data and process analytics, Artificial Intelligence & Machine Learning (AI/ML) and data reporting as part of their vision and roadmap.
Step 3: Customize and Configure the LIMS System
Collaborate with the selected vendor(s) to configure the LIMS to match your lab's specific workflows and processes – be wary of customization as it can be costly and impacts future upgrade paths and total cost of ownership (TCO). Tailor and configure the system to include relevant modules for sample tracking, results management, stability studies, and quality assurance checks. Ensure the LIMS system seamlessly integrates with existing instruments and laboratory equipment for efficient data capture. Consider the instruments' importance and plan to add them over time based on the value of the data and amount of times the instrument is used per day.
Step 4: Ensure Seamless Data Migration and Integration
Plan and execute the migration of existing data from legacy systems or paper records into the LIMS, ensuring data integrity throughout the process. Additionally, integrate the LIMS with other systems, such as the Enterprise Resource Planning (ERP) systems, to ensure data integrity and streamline data flow to support batch release. Collaborate with the vendor and/or a LIMS service provider to achieve these integrations, using industry-standard protocols and standard APIs for data exchange. Work closely with your IT and laboratory teams to thoroughly validate and test the data migration and integration processes, minimizing disruptions and errors. Finally, set up monitoring and maintenance procedures to ensure the smooth and continuous data flow between systems.
Step 5: Train Personnel for Effective LIMS Utilization
Provide comprehensive training to lab personnel on effectively using the LIMS. Cover essential areas such as sample registration, test execution, data entry, and generating reports. Emphasize the benefits of the LIMS system, such as improved efficiency, data traceability, and compliance with industry regulations. Offer ongoing support and additional training sessions as needed.
Step 6: Validate the LIMS System for Regulatory Compliance
Collaborate with the LIMS vendor, Service provider and Quality Assurance (QA) team to validate the system for regulatory compliance. Perform thorough testing and documentation to meet the stringent requirements of cGMP and other relevant regulations. Ensure the LIMS provides accurate and auditable results, adhering to data integrity and security guidelines. Ensure the QA team is involved in the project from the start and consider risk-based validation approaches to go faster.
Step 7: Go-Live
Plan a smooth transition from existing processes to the LIMS system, ensuring minimal disruption. Provide comprehensive technical support from initial to end phases throughout this transition and beyond. Monitor the system closely during the initial stages (hypercare) and seek continuous feedback from lab personnel.
Step 8: Continuous Improvement
Implement necessary refinements and improvements to optimize the system's performance, data management, and user experience. Continuous improvement is about enhancing the LIMS technical aspects and leveraging the data captured to facilitate data-driven decision-making. This approach can help identify areas for improvement in both business and laboratory processes, ensuring that the LIMS system evolves to meet your ever-changing needs. Additionally, consider incorporating data management principles and FAIR data (Findable, Accessible, Interoperable, and Reusable) to make your laboratory's data more valuable and accessible for analysis and support for decision-making.
Conclusion
Implementing a well-configured and tailored LIMS in manufacturing QC labs is critical to improving efficiency and ensuring data integrity & compliance. By following this step-by-step guide, labs can successfully generate value from LIMS. Our map ensures that:
- The entire batch release processes are considered and potentially optimized.
- Specific sample tracking and analytical testing results capture requirements are met.
- Lab processes are streamlined, simplified and optimized where possible.
- Accurate reporting and regulatory compliance are ensured.
- Process, data analytics and data interrogation are delivered as part of the environment.
If you want to know more about Zifo's experience supporting LIMS selections and rollouts in this domain, please email us at info@zifornd.com